12 Myths About Testing and Tagging Work Equipment Debunked
You might have heard a thing or two about testing and tagging work equipment. But what exactly is it? Do you need to do it? How often?
Testing and tagging Melbourne work equipment is the process of inspecting and testing electrical appliances and equipment to ensure they are safe to use. The frequency of testing and tagging depends on the environment in which the equipment is used – for example, office equipment may only need to be tested once a year, while construction site equipment may need to be tested every three months.
There are a lot of myths surrounding testing and tagging, so we’ve debunked 12 of the most common ones:
1. Only electrical equipment needs to be tested and tagged
Wrong! Any type of work equipment that plugs into an electrical outlet needs to be tested and tagged, including power tools, extension cords, and portable generators.
2. Testing and tagging are only required in certain industries
Nope! While there are some industries that are more regulated when it comes to testing and tagging (such as construction, mining, and healthcare), all businesses need to ensure their electrical appliances and equipment are safe to use.
3. Only new electrical equipment needs to be tested and tagged
Wrong again! All electrical appliances and equipment – regardless of age – need to be regularly inspected and tested to ensure they are safe to use.
4. Testing and tagging is a one-time process
Nope! Testing and tagging work equipment is an ongoing process – how often it needs to be done depends on the environment in which the equipment is used.
5. Once the equipment has been tested and tagged, it doesn’t need to be tested again
Wrong! Equipment should be regularly inspected for signs of wear and tear, and retested and retagged if necessary.
6. Only trained professionals can test and tag work equipment
While it’s recommended that only trained professionals carry out testing and tagging, there are some situations where untrained individuals can do it – for example, if the appliance is simple to use and test.
7. Testing and tagging is a time-consuming and expensive process
Testing and tagging don’t have to be time-consuming or expensive – they can be done quickly and easily and don’t require any special equipment.
8. All electrical appliances and equipment need to be tested and tagged
No! Only electrical appliances and equipment that are used in the workplace need to be tested and tagged. Appliances that are used at home, such as vacuum cleaners and hair straighteners, don’t need to be tested.
9. The testing process is complicated
The testing process is actually quite simple – it involves using a multimeter to test the appliance for signs of damage or wear and tear.
10. Testing and tagging are only required if the equipment is going to be used in a dangerous environment
Wrong! All workplaces have the potential to be dangerous, so all electrical appliances and equipment need to be regularly inspected and tested, regardless of the environment.
11. Testing and tagging are only required if the equipment is going to be used by multiple people
Nope! Any type of work equipment that plugs into an electrical outlet needs to be tested and tagged, regardless of who is using it.
12. Testing and tagging can be done by anyone in the company
While anyone in the company can carry out testing and tagging, it’s recommended that only trained professionals do it. This ensures that the job is done properly and safely.
Testing and tagging work equipment is important for ensuring a safe workplace. While there are some myths surrounding the process, it’s actually quite simple and straightforward. We hope that by debunking these myths, we can make testing and tagging less daunting for everyone.
If you have any questions about testing and tagging, or if you need help carrying out the process, please don’t hesitate to contact us. We’re always happy to help!
#testingandtaggingmelbourne
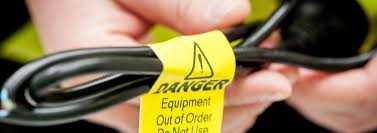